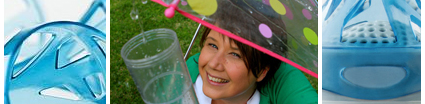
321 Water Product Commercialization
Collaboration
We worked with Gretha Oost, the Half a Teaspoon team and her suppliers to finalise the design, sort out the tooling issues and drive through to production the of the 321 Water Bottle. Getting involved in the product development at the tail end of a project is never an easy task for those involved but Bayly’s experience has proven invaluable.
Process
Bayly worked with different CAD data, toolmakers, materials and suppliers to correct and finalise aspects of the design produced by Half a Teaspoon working with another designer. We were involved in testing and refining off tool samples in an iterative process effectively managing the process to minimise time and cost impacts.
Innovation
A unique product producing very worthwhile outcomes does not come around very often.
Check out 321 Water at www.321water.com
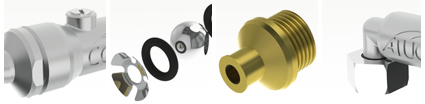
Connect Tapware fast with Non Return Flexi Valve™
Collaboration
Working with the Waterpex team (Part of the Couta Group) and their Chinese manufacurer to produce a compliant and cost effective product.
Process
Bayly developed the concepts from the Waterpex requirements and provided the 3D CAD and specifications for the Chinese manufacturer.
Innovation
The Non Return Flexi Valve meets a very specific need in the plumbing market. Our ability to produce the design suitable for hassle free manufacutre in China was a significant benefit to Waterpex. Products such as these are only feasible with low development costs.
Check out the full range of valves at www.waterpex.com.au
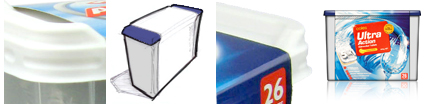
Coles Ultra Max
Collaboration
We worked with our client Cryovac to determine the requirements for the container in terms of its capacity, stacking, nesting, manufactured weight and materials, whilst ensuring that Coles marketing and logisitics requirements were acheived.
Process
Bayly worked on the concept design and development, the detail design and 3D CAD modelling of the container componets for production. Tooling was produced from the Bayly specifications without prototyping.
Innovation
The container incorporates injected moulded and thermoformed components. The design of the container is state of the art in terms of minimising the amount of raw materials used in it's manufacture.
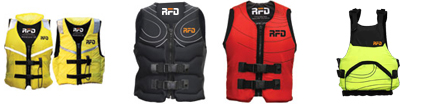
RFD Life Jacket Designs
Collaboration
We worked with the RFD teams in Australia, New Zealand, Northern Ireland and China to realise 10 new life jacket ranges of inherently buoyant and inflatable jackets to the updated requirements of AS 4758.
Process
Bayly worked on the concept design and development, the detail design and CAD modelling and prototyping to produce patterns, assembly drawings and complete BOM specifications for up to 9 different sizes in each range. The complete specifications for the jackets were managed in Bayly's product lifecycle management (PLM) system. Extensive use of Bayly's collaboration systems were required to facilitate communication between the team members. Bayly worked directly with RFD's joint venture manufacturing partner in China to resolve issues in pilot production and continue to provide support during manufacture.
Innovation
The Level 100 life jacket range includes products tailored specifically for female users. The designs of the jackets across the ranges project a uniformity of key design attributes and common elements that reinforce their belonging to the RFD brand. Through the selection of different materials, features and manufacturing details, RFD are able offer differently priced products to the market; providing a greater range of choice to the consumer.
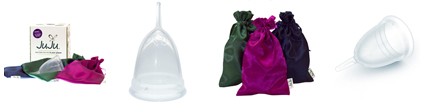
Ju Ju
Collaboration
We worked with Brenda and Katryna of Freedom Products to produce a design for the juju cups. Anthropometric data from our associates at Mark Dohrmann & Partners was used to confirm important sizing specifications for the products. We tested and reviewed competitors products in combination with finite element analysis of our designs to fine tune the performance of the cup; to minimise leakage and optimise ease of insertion. We worked with Romar Engineering in the development of materials and tooling for the production of the cups.
Process
Bayly worked on the concept design and development, the detail design and 3D CAD modelling of the cups for production. Tooling was produced from the Bayly specifications.
Innovation
The cup is produced from injected moulded medical grade silicone rubber. Persistent branding of the product is moulded into the cups. Small pressure release features have been included in the design to facilitate insertion and removal.
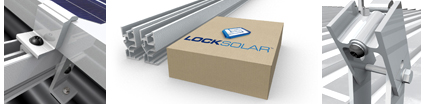
Lock Solar
Collaboration
We worked with Lock Solar to ensure that the Rack in a box® range would suit domestic installations around the country and comply with Australian standards for environmental loading and structural design.
Process
Bayly worked on the concept design and development, the detail design and 3D CAD modelling of the system and its components for production. Extrusion tooling was produced from the Bayly specifications without prototyping. Bayly produced the structural design to Australian standards. The installation manuals were also produced by Bayly.
Bayly produced an animation that Lock Solar could use on its website to highlight the simplicity and functionality of the Rack in a box® system.
Innovation
The mounting system incorporates extruded and machined aluminium components and stainless steel fasteners. The design of the Rack in a box® system is state of the art in terms of minimising the amount of raw materials used in it's manufacture.
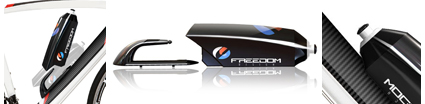
Freedom Bike Bottle
Collaboration
We worked with Steve to realise his idea and in doing so designed a bottle and holder system that can be manufactured using common and standard manufacturing techniques at a reasonable cost.
“Bayly worked with me and my partners to prove the concept, identify the parameters and characteristics of the Freedom Design and then provided concepts and prototypes to fire the imaginations of my potential licensees. To show them what could be and let me get the deals done.” - Steve Serpell, Freedom Design
Process
Bayly worked on the concept design and development, the detail design and 3D CAD modelling and manufacture of prototypes of the different bottle designs using a common mounting pin so that licensees of the designs and technology could be arranged.
Innovation
The Freedom Design solution is characterised by the use of a novel internal fastening technique of the water bottle to the holder. Simple and brilliant. The shape of the bottle is no longer mandated to be cylindrical. Now bottle and bicycle manufacturers can customise the bottle design in different ways to improve the aesthetic and aerodynamic attributes of the bike. Branding on the bottle is no longer destroyed as the bottle is used. Bottles retain their finish and markings longer and improve the durability of the product. The ease of use of the system has been dramatically improved. The bottle only needs 25mm of parallel travel before it can be moved laterally and removed from the bike. Less precision is required in replacing the bottle and this makes the task easier and quicker. The design of the bottle and holder provides a means for securely locking the bottle in place and prevents rattling and vibration.